Omron Servomotors
Omron Servomotors and Servo Drivers are provided for the purpose of high-speed, high-precision control.
The G5 series has a direct connection to the NJ controller via EtherCAT. Customers can design faster, more advanced machine automation control systems.
- High-accuracy positioning with fully-closed control.
- Servo Drives for 400VAC globally widens applicable systems and environment, including large-scale equipment.
- Safe design and Safe Torque Off (STO) function.
- Vibration can be suppressed in acceleration/deceleration even in low-rigidity mechanical systems.
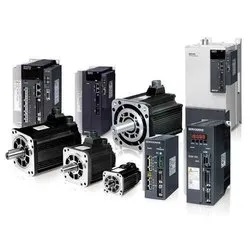
G5 Series 0.1kW ~ 15kW (Standard or with Brake)
Servo Amplifier – R88D-K (1ph or 3ph 200V)
Servo Motor R88M-K 0.1kW ~ 15kW
Encoder Cable (Standard) 5meter Length – R88A-CRGB005C
Power Cable (Standard) 5meter Length – R88A-CAGA005S
General Purpose Control Cable (Standard) 5meter Length – R88A-CPG001S
Brake Cable (Standard) 5meter Length – R88A-CAGA005B-MY
OMRON PLC CJ2/CJ1 series
OMRON Positioning Module CJ1W series
High-Speed and High-Precision G5 Series EtherCAT Communications with the Controller
- High-accuracy positioning with fully-closed control.
- Servo Drives for 400VAC globally widens applicable systems and environment, including large-scale equipment.
- Safe design and Safe Torque Off (STO) function.
- Vibration can be suppressed in acceleration/deceleration even in low-rigidity mechanical systems.
Please check OMRON official website for the lineup of industrial components and their datasheets that OMRON corporation provides on a global basis.
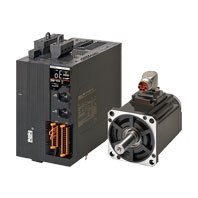
AC Servo System 1S-series with Safety Functionality
R88M-1A[] / R88D-1SAN[]-ECT
Safer environment and higher productivity
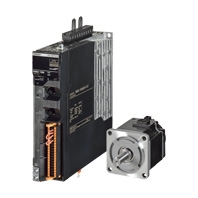
AC Servo System 1S-series
R88M-1[] / R88D-1SN[]-ECT
Optimized installation and setup Increased machine productivity

G5 Series AC Servomotor/Servo Drives with built-in EtherCAT Communications
R88M-K, R88D-KN[]-ECT
The G5 series has a direct connection to the NJ controller via EtherCAT. Customers can design faster, more advanced machine automation control systems.
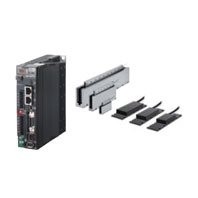
G5 Series Linear Motor/Servo Drives with built-in EtherCAT Communications Linear Motor Type
R88L-EC, R88D-KN[]-ECT-L
Linear Motor for Higher-speed and Higher-precision
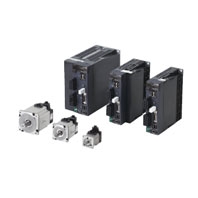
G5-series AC Servomotors/Servo Drives with Built-in MECHATROLINK-II Communications
R88M-K, R88D-KN[]-ML2
MECHATROLINK-II network communication modules are now available for the G5 series.
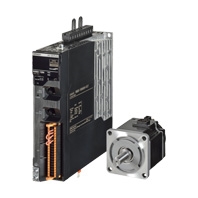
AC Servo System 1S-series
R88M-1[] / R88D-1SN[]-ECT
Optimized installation and setup Increased machine productivity
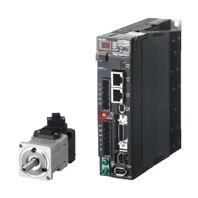
G5 Series AC Servomotor/Servo Drives with built-in EtherCAT Communications
R88M-K, R88D-KN[]-ECT
The G5 series has a direct connection to the NJ controller via EtherCAT. Customers can design faster, more advanced machine automation control systems.
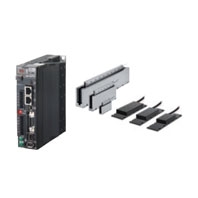
G5 Series Linear Motor/Servo Drives with built-in EtherCAT Communications Linear Motor Type
R88L-EC, R88D-KN[]-ECT-L
Linear Motor for Higher-speed and Higher-precision
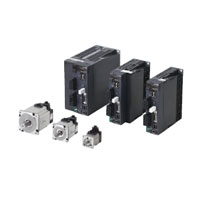
G5-series AC Servomotors/Servo Drives with Built-in MECHATROLINK-II Communications
R88M-K, R88D-KN[]-ML2
MECHATROLINK-II network communication modules are now available for the G5 series.
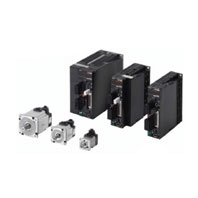
G5-series AC Servomotors/Servo Drives with General-purpose Pulse Train or Analog Inputs
R88M-K, R88D-KT
Pulse and analog input modules are now available for the G5 series.
G Series Solutions :
Let the G Series solve your equipment problems!
- Increase Productivity
The many variations provided by G-series Servo Motors and Servo Drivers features high-precision positioning with improved response and vibration control, making it suitable for a variety of applications. - Integrated Development Environment Cut Your TCO from Design to Maintenance
MECHATROLINK-II-compatible AC Servo Motors / Servo Drivers
One Cable Enables Setting and Monitoring Parameters
Connect the PLC and Servo Driver with a single cable to reduce wiring. What’s more, the parameters for many Servo Drivers can be set and monitored at the same time between a personal computer and the Controller. - Easy Adjustment
Realtime autotuning sets the optimum gain.
An autotuning function calculates the device load in realtime and automatically sets the optimum gain, simplifying the adjustment procedure. - Reduce Tact Time
Significantly better speed response frequency.
The speed response frequency has been improved by a factor of 2.5 compared to previous OMRON models. (See note.) The stabilization time has been reduced, increasing machine speed and response performance. - Reduce Mechanical Vibration
Quick suppression of vibration with an adaptive filter.
Even if the resonant frequency changes, realtime evaluation automatically follows the changes to reduce the effect of vibration due to low mechanical rigidity, such as for conveyer belts.