Pressure Sensor is an important device in many fields such as industry, medicine, daily life. This device measures the pressure of liquids or gases in different systems. This article of FLEXTECH will provide detailed knowledge about Pressure Sensor from concept, and structure to practical application.
What is a Pressure Sensor?
A pressure sensor is a device that converts pressure (usually the pressure of a liquid or gas) into a measurable electrical signal. This electrical signal can be a voltage, a current, or a change in capacitance or resistance.
These sensors play an important role in a wide range of applications, from medical and industrial to automotive and aerospace.
How many parts does a Pressure Sensor consist of?
A Pressure Sensor consists of the following 4 main parts:
- Sensing Element: This is the most important part, responsible for converting pressure into a physical signal (usually electrical). This element can be made from different materials such as Piezoelectric Sensor, Strain Gauge Sensor, Capacitive Sensor, … depending on each application
- Sensor Diaphragm: The sensor membrane is the part that is in direct contact with the pressure environment to be measured. When pressure is applied to the membrane, it will deform and transmit this force to the sensor element.
- Signal Transducer: This part is responsible for converting the physical signal from the sensor element into an electrical signal (analog or digital) to be transmitted to the control system.
- Protective housing: Usually made of metal, silicon or ceramic, helping to protect the internal components from external factors such as dust, water, temperature, and corrosive environments.
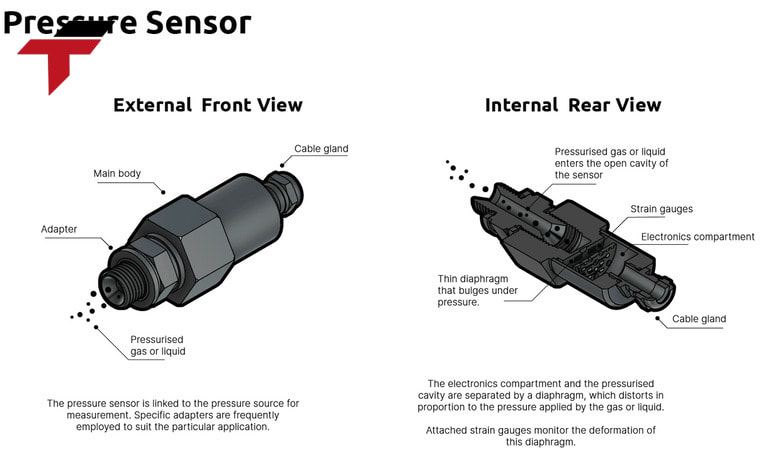
Structure of Pressure Sensor
What are the common types of Pressure Sensors?
There are many different types of pressure sensors, each with its own operating principle and application. Here are some of the most common types:
Piezoelectric Pressure Sensor
- Operating principle: Piezoelectric sensors use the piezoelectric effect, whereby certain materials will generate an electric charge when subjected to pressure.
- Advantages: High sensitivity, good frequency response, can measure dynamic pressure.
- Disadvantages: High cost, difficult to use in high temperature environments, cannot measure static pressure.
- Applications: Measuring pressure in internal combustion engines, studying ultrasonic waves, measuring vibration pressure.
Strain Gauge Pressure Sensor
- Operating principle: Resistive sensors are based on the principle that when a material is deformed by pressure, its resistance also changes.
- Advantages: High accuracy, can measure both static and dynamic pressure, relatively reasonable price.
- Disadvantages: Sensitivity is not as high as piezoelectric sensors, affected by temperature.
- Application: Measure pressure in hydraulic, pneumatic, electronic scales systems.
Capacitive Pressure Sensor
- Operating principle: Capacitive sensors measure pressure by changing the distance between the two electrodes of the capacitor when pressure is applied.
- Advantages: High sensitivity, less affected by temperature, high durability.
- Disadvantages: Complex circuit, higher price than resistive sensors.
- Application: Measure pressure in car brake systems, medical equipment, industrial machinery.
Piezoresistive Pressure Sensor
- Operating principle: Similar to resistive sensors, but uses semiconductor materials with large resistance changes when pressure is applied.
- Advantages: High sensitivity, compact size, low power consumption.
- Disadvantages: Affected by temperature, cannot measure high pressure.
- Application: Measure pressure in mobile devices, tire pressure monitoring system (TPMS).
Resonant Pressure Sensor
- Operating principle: This sensor uses the resonance frequency of a mechanical structure to measure pressure. When the pressure changes, the resonance frequency also changes.
- Advantages: Very high accuracy, less affected by temperature, can measure both static and dynamic pressure.
- Disadvantages: Very high price, complex circuit.
- Application: Measure pressure in harsh environments, applications requiring high accuracy such as aerospace.
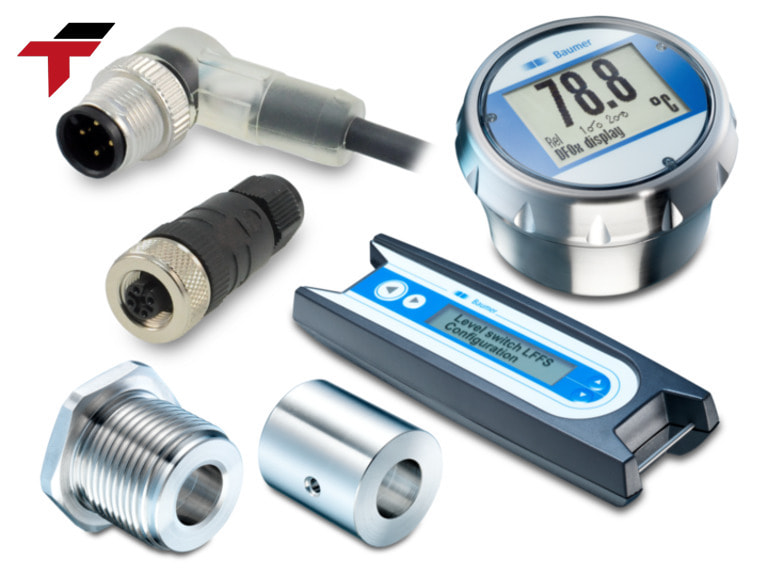
Pressure Sensor is classified into 5 main types
What are the benefits of using a Pressure Sensor?
Using this sensor not only improves performance but also optimizes costs and ensures safety. Here are some of the outstanding benefits of using a pressure sensor:
- Accurate data measurement: Pressure sensors provide accurate pressure measurement with low error, meeting the strict requirements of many industries such as oil and gas, chemicals, food, and pharmaceuticals.
- Increased operational efficiency: The sensor’s output signals can be sent directly to the PLC controller or SCADA system, allowing management and adjustment of equipment such as pumps, valves, or fans to maintain stable pressure, optimize energy, and increase productivity.
- Timely warning: When the pressure in the system exceeds or drops below the allowable level, the sensor will send a warning signal to the control system, helping to prevent serious incidents such as pipeline explosions, equipment failure, or the risk of work accidents.
- Reduced operating costs: Pressure sensor-integrated systems typically require less human intervention, reducing labor costs and minimizing system downtime.
What are the considerations when choosing a Pressure Sensor?
Choosing the right pressure sensor is very important to ensure the efficiency of the system. Here are some factors to consider:
Type of environment
Consider whether the environment is used with chemicals, humidity or corrosive factors to choose a sensor with the right material.
Choose the right pressure measuring range
If the measuring range is too low, the sensor is susceptible to damage when the pressure exceeds the threshold. Conversely, if the measuring range is too high, the ability to accurately measure within the required pressure range will be reduced.
Choose the type of output signal
For traditional systems, analog signals such as 4-20mA or 0-10V are popular choices because of their simplicity and ease of integration.
Meanwhile, digital signals such as RS485 or Modbus are more suitable for modern systems, allowing long-distance data transmission and integration with many other devices in the automation network.
Sensor Accuracy
For industries requiring high accuracy such as pharmaceuticals or oil and gas, sensors with ±0.1% accuracy are the optimal choice. Meanwhile, general industrial applications can accept ±1% accuracy to save costs while still meeting measurement needs.
By carefully considering the above factors, you can choose the right pressure sensor, ensuring operational efficiency and optimizing costs for your system.
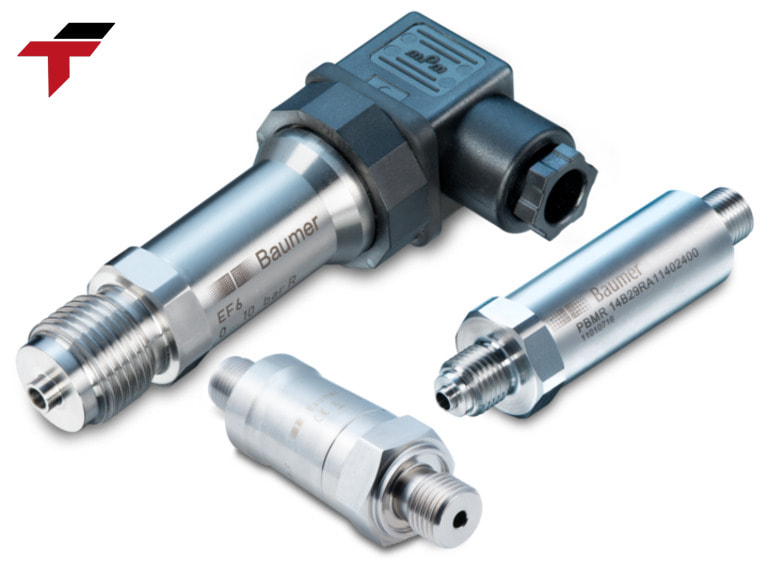
Important notes to choose the appropriate Pressure Sensor
Conclusion
Pressure sensors play an indispensable role in modern life, widely used in many different fields. Understanding the operating principles, types of sensors, and how to choose them is very important for effective application in work and life. Hopefully this article has provided you with useful information about pressure sensors.