Rotary Encoder is an important device in automation systems, helping to accurately measure and monitor rotary motion. Although widely used in many industries, selecting and using a suitable Rotary Encoder depends on many factors such as working environment, accuracy requirements, and technical features.
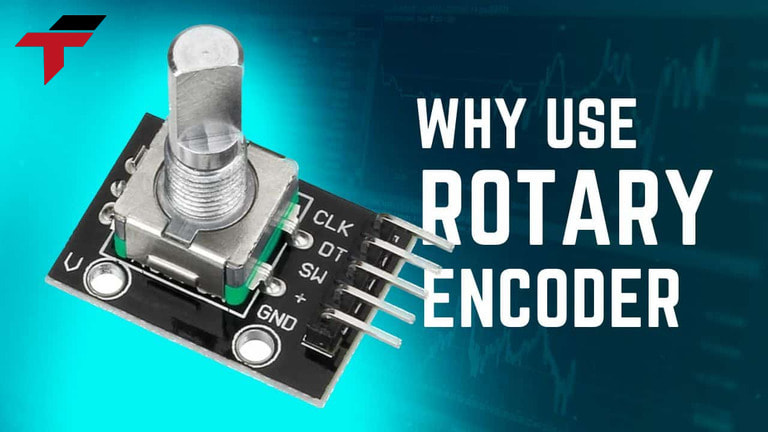
Introducing Rotary Encoder
Introduction to Rotary Encoder
A Rotary Encoder, also known as rotary encoder, is a sensor device used to measure the position, speed, or direction of rotation of a motor shaft or other rotating mechanism. This device converts mechanical motion into electrical signals to provide precise data for control systems in automated production lines.
Rotary Encoder is commonly used in many industries, including automation, robotics, mechanical processin,g and packaging. With the ability to provide pulse or absolute signals, this device ensures accuracy and flexibility in motion control.
How many parts does a Rotary Encoder consist of?
The rotary encoder consists of the following 3 main parts:
- Encoder disc: This is a circular disc attached to the rotating shaft. The disc has special lines, grooves or patterns. These patterns can be created by printing, engraving or using other methods.
- Sensor: The sensor is placed near the encoder disc and is responsible for detecting changes when the lines or patterns on the disc move across. There are many different types of sensors, the most common being optical sensors, magnetic sensors and capacitive sensors.
- Signal processing circuit: This circuit will convert the signal from the sensor into a usable electrical signal, usually in the form of pulses. These pulses can be counted to determine the angular position or the pulse frequency to determine the rotation speed.
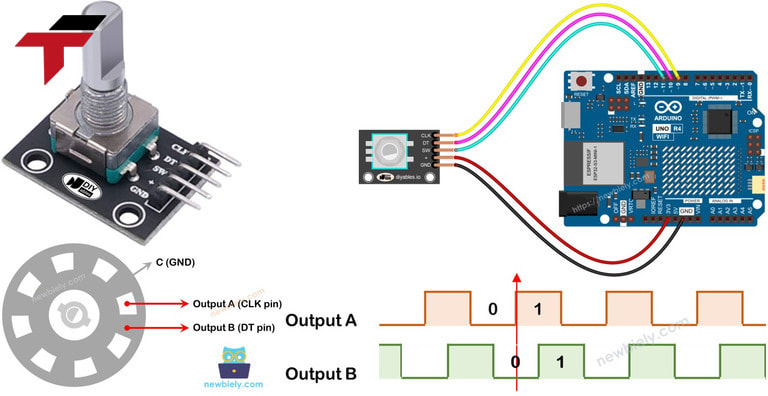
Structure of Rotary Encoder
How many types of Rotary Encoder are there?
Rotary encoders are classified based on a variety of criteria, most commonly based on the measurement method and technology used.
Based on the Measurement Method
- Absolute Encoder: The device provides a unique position value at every angular position. This means that each angular position has a unique, non-repeating binary code.
- Incremental Encoder: An incremental encoder only generates pulses as the shaft moves. It does not provide an absolute position value, but only indicates a change in position.
Based on Technology
- Optical Encoder: Uses a light source (usually an LED) and a photodiode to detect lines or grooves on the encoder disk. As the disk rotates, light is blocked or passes through the lines, creating electrical pulses.
- Magnetic Encoder: Uses a magnet mounted on the encoder disk and Hall sensors to detect changes in the magnetic field as the disk rotates.
- Capacitive Encoder: Uses the change in capacitance between electrodes on the encoder disc and the sensors to detect rotational motion.
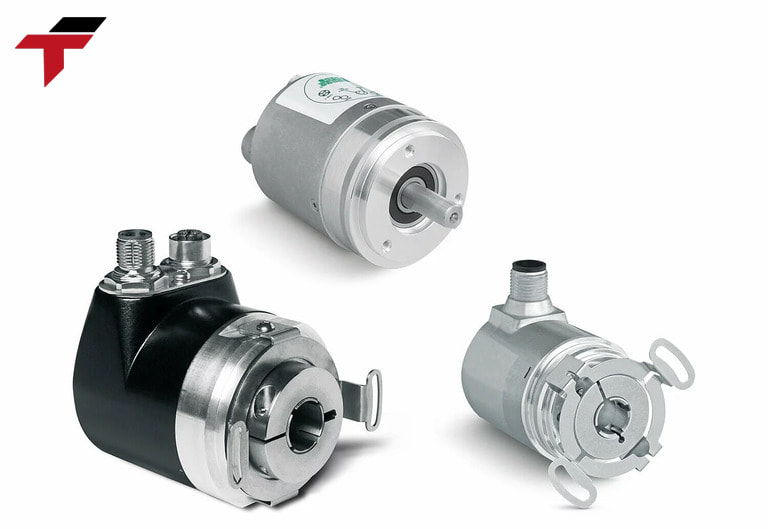
Rotary Encoder is divided into many different types
Why should a Rotary Encoder be used in the production line?
In modern automation and manufacturing systems, precise motion monitoring and control is a key factor in ensuring performance and quality.
Rotary Encoder, as a rotary motion measurement device, not only provides reliable data but also brings many practical benefits to businesses.
Below are the outstanding benefits that Rotary Encoder brings in the process of operation and production management.
- Precise measurement: The Rotary Encoder provides precise data on speed, position, and direction of rotation, helping to improve the performance and accuracy of automation systems.
- Increased operational efficiency: Encoder supports real-time motion monitoring and control, helping to optimize the operation of machines and production lines.
- High integration capability: The device is easily connected to control systems, such as PLCs or industrial computers, creating system flexibility and scalability.
- Support smart management: With the ability to provide real-time data, encoders help businesses apply automation technology and smart management in production.
- Improve safety: Accurate data from encoders helps closely monitor movements, reducing the risk of damage or accidents during operation.
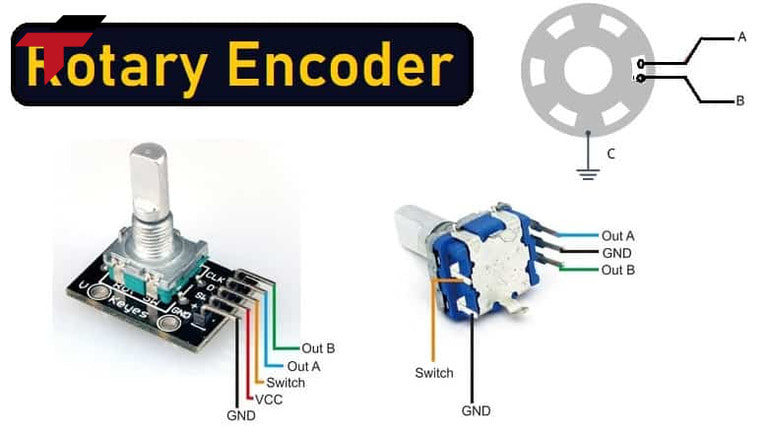
Rotary Encoder brings many benefits to businesses
What are the disadvantages of Rotary Encoder?
Although Rotary Encoders offer many benefits in automation and manufacturing applications, not all devices are perfect. Like any technology, Rotary Encoders have disadvantages that should be considered before deciding to use them.
Below are some disadvantages that businesses should be aware of when choosing and implementing Rotary Encoders in their systems.
- Stable power supply requirements: Rotary Encoders require a stable power supply to operate properly. Any changes or power outages can disrupt the signal and cause data loss, especially with absolute encoders.
- Correct installation requirements: The encoder installation must be coaxial with the rotating shaft to avoid errors and damage. The distance between the encoder disk and the sensor must be kept within the allowable range to ensure the sensor can read the signal accurately.
- Temperature and humidity limits: Encoders often have operating temperature and humidity limits. If this limit is exceeded, they may operate incorrectly or become damaged. Regular maintenance and cleaning are necessary to ensure stable operation.
What to consider when choosing a Rotary Encoder?
- Determine the purpose of use: Businesses need to clarify the need to use the encoder, such as measuring speed, relative or precise position. This helps determine the appropriate type of device to meet the requirements of efficient operation.
- Working environment: The encoder needs to be suitable for working conditions, including temperature, humidity, and dust levels. Devices that are water or dust resistant will be suitable for harsh environments.
- Output signal type: Businesses need to check the current control system to choose a compatible output signal type, such as analog or digital signals.
- Budget and brand: Choosing encoders from reputable brands helps ensure durability and technical support. However, businesses should also consider the budget to choose the right solution without exceeding the expected cost.
- Connection form: The encoder must be compatible with the existing connection system. Connection types such as wires, signal ports or wireless protocols need to be carefully evaluated before purchasing.
Choosing the right Rotary Encoder will help businesses optimize efficiency and ensure accuracy in manufacturing applications.
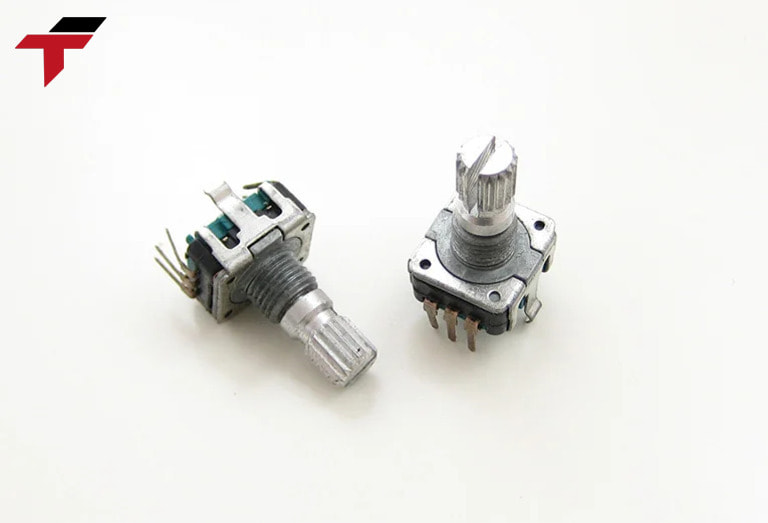
Notes when buying Rotary Encoder
Conclusion
Rotary Encoders play an important role in the field of automation, helping businesses improve efficiency, and accuracy and optimize production processes. With many types and features suitable for each application, choosing the right Rotary Encoder not only ensures stable operation but also brings long-term economic and technological value.
Investing in this measuring device is a smart step to meet the increasing demands of modern industry.